Restricted content
October 5, 2023Electrical,Equipment,Regulations & Standards
connecting our industry
Technical Guidance Document #055
Following a recent tragic fatal electrocution of a technician in our industry, ceda believe it is appropriate that we issue a reminder note on basic electrical safety in the work place.
Published October 2023
Download Link:
Guidance Document No 55 – Electrical Safe Working
Restricted content
July 24, 2023Electrical,Equipment,Regulations & Standards
connecting our industry
Technical Guidance Document #053
This guidance document has been published following the results of a prosecution by HSE relating to the tragic death of an engineer when working on a waste disposal unit where both the manufacturer and the company who installed the appliance were found guilty.
Published July 2023
Download Link:
Guidance Document No 53 – Best Practice When Installing Or Working On Electrical Equipment V3
Restricted content
January 25, 2024Electrical,Equipment,Regulations & Standards
connecting our industry
Technical Guidance Document #050
Waste disposal units have long been an accepted tool for the hygienic disposal of food waste and operate by grinding the food waste into small particles in a flow of cold water before flushing them down the drain.
Published January 2024
Download Link:
Guidance Document No 50 – Waste Disposal Units
First time fix rate is a higher priority than time-based SLAs
First time fix rate is a higher priority than time-based SLAs
Given today’s fast-changing environments where catering service and maintenance is provided, service level agreements (SLAs) between customers and third-party service providers often can drive the wrong outcomes.
Following the challenges and changes of the pandemic, alongside the ever growing issue to supply chain and parts availability – in a number of cases metrics that have been previously used to judge whether a service provider such as the service and maintenance of catering equipment, have become completely irrelevant.
The message from our team at HOBART Service is clear – is it now time to review and rethink your SLAs?
As a market leading commercial catering equipment and service provider, we understand the importance of mitigating any downtime. We believe that when a piece of equipment breaks down, the critical factor is the time it takes to fix the equipment, not the time it takes for a technician to arrive on site.
However, other providers promise quick-reaction SLAs, and meet them, yet are not always in a position once they arrive on site to provide a fix. This can result in equipment standing dormant for days while parts are ordered or waiting for a more qualified technician, bringing operations to an abrupt halt.
We recently spoke with Armend Aljo, Procurement Manager at Oakman Inns and Restaurants who commented:
“Downtime would be a huge issue for our businesses as it immediately affects service delivery to our customers.”
“A 4-hour reaction time literally only works on paper in my opinion. Because you can have somebody jump in a van and go to site and look at a problem, agree a part is needed which will take 3 or 4 days and then they leave… you pay a premium for the 4-hour reaction time and get nothing in return.”
“When it comes to a 4-hour reaction time which some companies require, it is all blown out of proportion as to what really matters – which is the fix. Something that HOBART Service have always achieved for us due to being the service delivery team for the manufacturer.”
HOBART Service advise any businesses who are currently under a time-based call out SLA, yet experiencing issues such as first time fixes or parts availability, to revisit the contract and SLA regularly, whilst discussing and exploring what is business critical.
Response times simply state how quickly the service provider must respond to your report of a problem (even if just to confirm receipt of your request).
Repair times (deadline for the problem to be fully solved) also tend to be stated as non-binding targets, or sometimes, are left out entirely.
Customers need an approximate deadline for solving problems. Vendors may explain that repair times are purposely omitted because they cannot estimate repair time until they know the root cause, however, no matter the cause, you are paying for a service you are not getting; therefore, it is entirely reasonable for you to ask for a repair deadline, with a remedy if missed.
For further information about HOBART Service plans, which include three levels of service and maintenance support to suit your requirements and budget please visit https://www.hobartuk.com/service/overview or call 0844 888 7777.
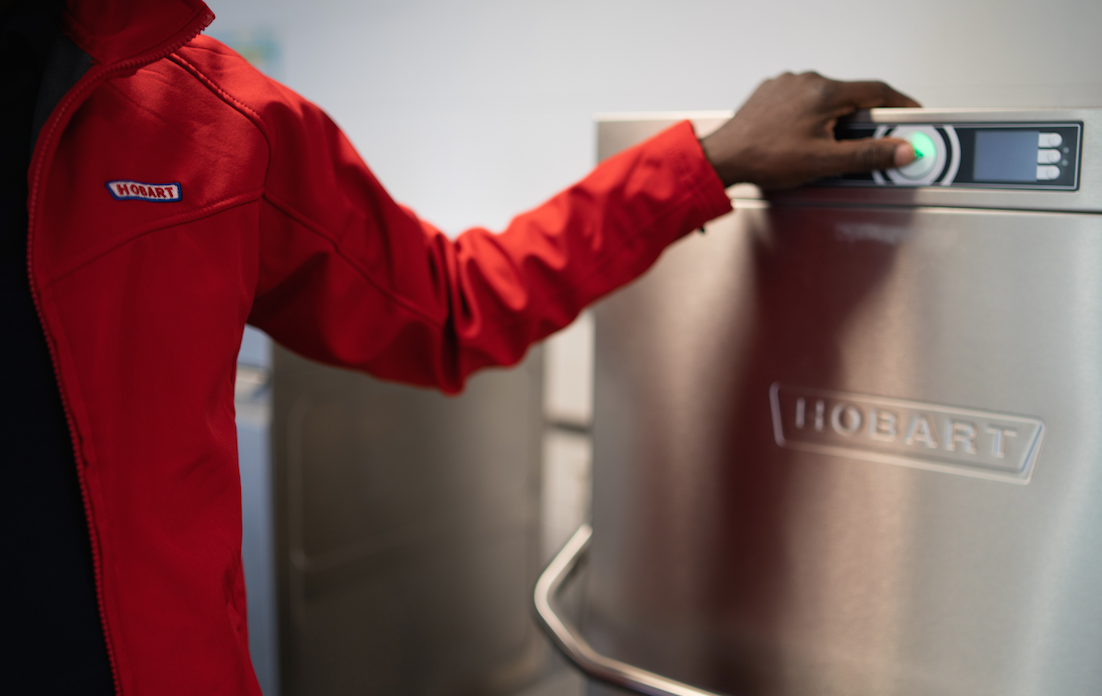
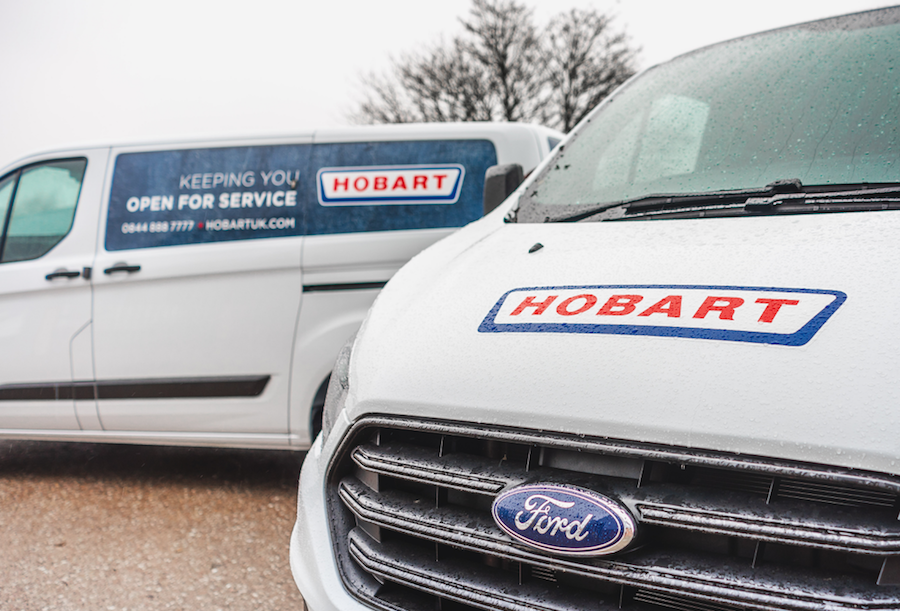
Restricted content
July 24, 2023Electrical,Equipment,Regulations & Standards
connecting our industry
Technical Guidance Document #051
A Minor Electrical Works Certificate should be issued when any work is carried out that involves an addition to, or alteration of, an existing electrical circuit and that does not impair the safety of the existing circuit.
Published July 2023
Download Link:
Guidance Document No 51 – Minor Electrical Works Certificates
Restricted content
December 6, 2022Gas,Equipment,Regulations & Standards
connecting our industry
Technical Guidance Document #049
IGEM UP/19 is the standard that relates to the design and application of gas interlocks in commercial catering kitchens installations.
UP/19 was first published by IGEM in 2014 and amended in January 2015. In line with normal review processes, it has been updated in 2022.
Published December 2022
Download Link:
Guidance Document No 49 - IGEM UP/19 Edition 2 update
Restricted content
July 24, 2023Electrical,Equipment
connecting our industry
Technical Guidance Document #052
Before commencing work on any appliance that is connected to an electrical supply it is essential to test that the appliance itself and any metal piping or tabling that is connected to it is tested to ensure that it is not live due to an electrical fault. Indeed, due to several fatalities over the years, it has become custom and practice within the gas industry to use a single-pole or no-contact live-circuit detectors (sometimes referred to as Voltage Sticks).
Published July 2023
Download Link:
Guidance Document No 52 - Testing for ‘safe to touch'
Restricted content
September 12, 2022Electrical,Equipment
connecting our industry
Technical Guidance Document #047
Whilst European plugs do have an earth connection, this is in the form of a metal strip within the body of the plug which only connects the earth when the plug is connected to a matching socket which has an internal earth terminal that connects with the strip connector in the plug. See picture below. This means that when connected using a travel adaptor of the type shown in this case, the appliance is not earthed.
Published September 2022
Download Link:
Guidance Document No 47 - Appliances fitted with 2 European pin plugs
Restricted content
November 1, 2022Ventilation,Equipment
connecting our industry
Technical Guidance Document #048
Trials are progressing to investigate the suitability of Hydrogen as a replacement for natural gas. Initially Hydrogen will be blended with natural gas in the ratio of 20% Hydrogen and 80% natural gas and it will not have any impact on ventilation requirements, however, 100% Hydrogen is also being trialled and will no doubt be introduced in some parts of the country within a few years.
Published November 2022
Download Link:
Ventilation in kitchens using Hydrogen Interim Guidance
It’s a Gold investment!
It's a Gold Investment
Staff at Rational UK, the leading provider in hot food preparation cooking systems are celebrating their Gold accreditation recently awarded by Investors in People. Only 17% of Investors in People accredited organisations achieve Gold.
A Gold accreditation means that Rational UK have all the required policies in place but more than that, it means everyone within the business take ownership for making them come to life.
Rational the leading provider in hot food preparation equipment, would not be what it is today without its employees. Every employee is encouraged to act as an independent entrepreneur in the company – working with dedication, responsibility and in the interest of the entire company. This approach seems to be on point, as 97% of their UK employees said that they are proud to be working for Rational.
Paul Devoy, CEO of Investors in People, said: “We’d like to congratulate Rational UK. Gold accreditation on We invest in people is a fantastic effort for any organisation, and places Rational UK in fine company with a host of organisations that understand the value of people.
Commenting on the award, Helen Varley, People Manager, RATIONAL UK, said: “Here at Rational we are delighted to receive this prestigious award. The UK team consists of 60 experienced and professional individuals, who have had a part to play in the assessment; from taking part in a survey, attending a leadership context meeting presenting an overview of the business and evidence in relation to the performance indicators, to attending one-to-one assessor interviews.”
The Rational guiding principles and values permeate every aspect of its culture and ways of working. Providing maximum customer benefit has always been the company’s main mission. This is not limited to their external customers but also to colleagues and friends that they work alongside daily. Rational continue to focus on providing maximum customer benefits, keep making changes, keep improving and keep moving forward to improve the lives of both their internal and external customers.
Investors in People believe that the success of organisations begins and ends with people, “If we make work better for everyone, we make work better for every organisation. And if we do that… we make society stronger, healthier and happier.” Readers can find out more about Investors in people at: www.investorsinpeople.com
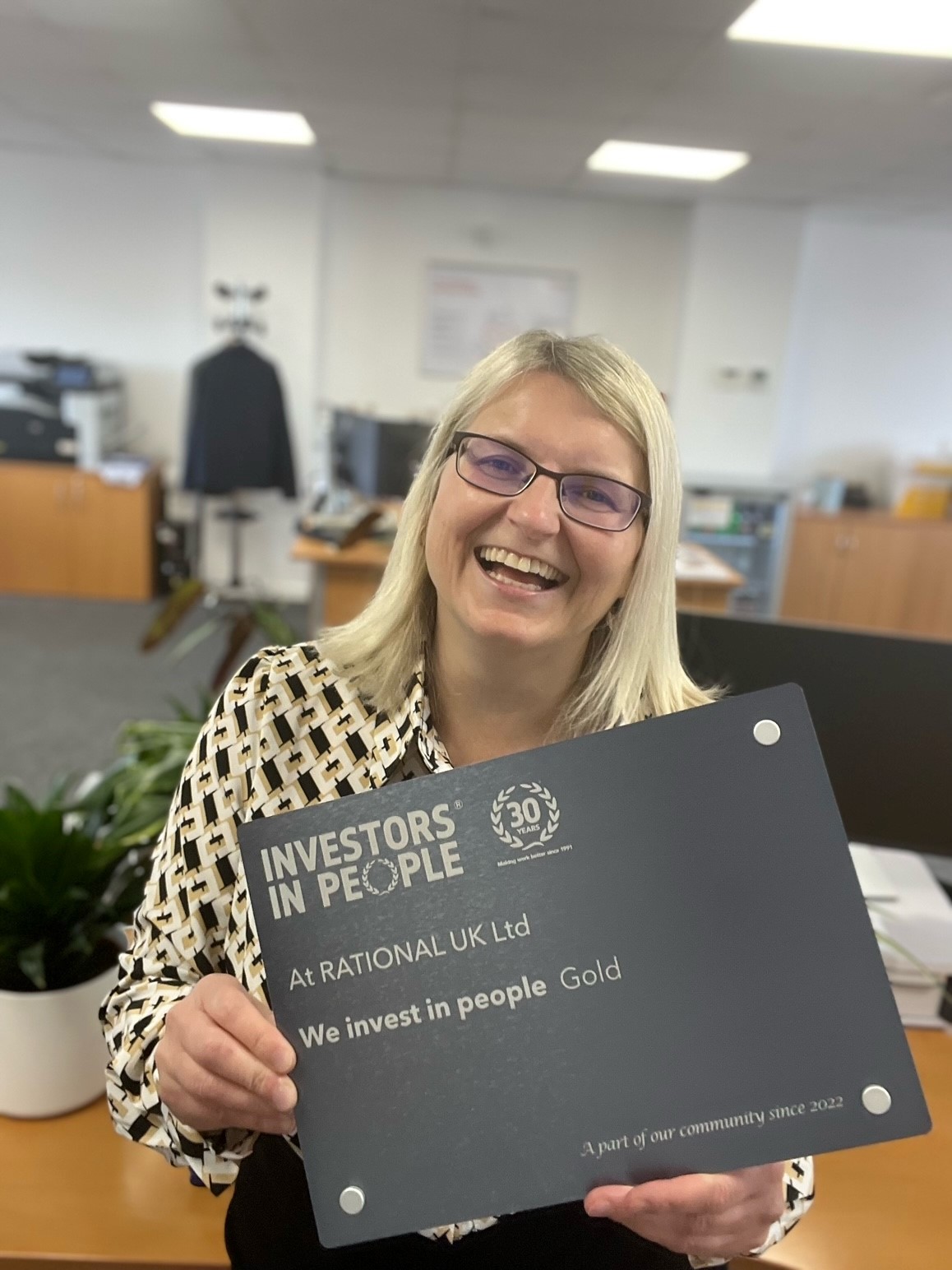