ceda Partner First Choice Group secures approved partner status on 3M Water Filtration portfolio
ceda Partner First Choice Group secures approved partner status on 3M™ Water Filtration portfolio
Adding to its extensive list of Master Distribution Partners (MDP), ceda Approved Partner First Choice Group is proud to announce that it has become an official approved supplier of OEM water filters from leading brand, 3M™.
With over 60% of businesses in the UK being impacted by limescale, the 3M™ range combines multiple technologies developed over many years of experience in the foodservice sector, to remove the unwanted impurities found in water. Protecting valuable beverage equipment, including the latest coffee and hot beverage units, 3M™ water filters have been found to improve customer satisfaction and generate repeat business by delivering of high quality hot and cold beverages.
In addition to the hot beverage range, First Choice stock list includes 3M’s ice machine and cold beverage equipment specific filters, it is clear that great water makes great ice, and that is why the filters help, by removing excess sediment, inhibiting the build-up of scale and ultimately reducing downtime of your machine. Leading to significantly better looking and tasting ice, customers can enjoy their drinks just how you intended to serve them.
When it comes to cold beverage equipment, not only do unwanted particulates significantly reduce the service life of expensive cold beverage equipment, but they can also have a detrimental effect on the look and taste of the customer’s beverage. The 3M™ Water Filtration products are available to suit a range of cold beverage needs, including carbonated systems, high flow rate pumps and even to suit the quality of a site’s local water supply.
Alternatively, the 3M™ ice machine specific filters have been created to keep your ice machine in top condition, crucial to maintaining efficiency and to give customers the very best chilled beverage experience. The 3M™ range is suitable for many of the most popular cuber, flaker and nugget machines on the market, they have been proven to reduce waterborne bacteria by 99.9%* and they can significantly reduce the corrosion caused by residual chlorine and scale build-up.
As a complete one stop solution, First Choice Group is the UK’s largest stockist of OEM spare parts, providing customers with direct access to thousands of genuine products from hundreds of leading equipment manufacturers at competitive prices. With our logistical solutions including same day dispatch (on orders placed before 7pm) and next-day delivery as standard for mainland UK orders, tailoring our service to meet the specific demands of the foodservice industry.
In addition to purchasing 3M™ Water Filtration products using its ecommerce website, customers can harmoniously shop from any location by using the First Choice Catering Spares app, with features including intuitive text, voice search, 360° images, and fast, secure checkout facilities.
On the announcement, Steven McLaren, Head of Manufacturer Partnerships at First Choice Group commented:
“We are delighted to be working with 3M™ Water Filtration as their official distributor to the Foodservice market. Not only does this give direct access to a much more competitively priced product range, which will benefit our customers, but we also have direct access to the knowledge professionals at 3M™ and the fantastic distributor support they provide across many areas. We look forward to a partnership where we both develop positively through 2021 and beyond.”
Confirming the latest partnership with First Choice Group, Cheryl Thomas, Channel Manager at 3M™ explains:
“It is crucial for 3M™ that we have confidence in the quality of our supply chain, the First Choice Group allows us to enhance our offering using their state of the art ecommerce capability along with their technologically advanced mobile app. Our customers can quickly and efficiently purchase water filters from our ranges including, ice, cold beverage, coffee, espresso, hot and cold water knowing the level of technical knowledge and customer service offered by the First Choice Group is exemplary.”
First Choice Group prides itself on our award-wining customer service, the ease of access to the necessary technical and supporting documents and of course, our commitment to offering our customers the best, genuine OEM spare parts. The partnership with 3M™ allows it to give direct access to the company’s Water Filtration products, including same day dispatch and next day delivery as standard (on orders placed before 7pm weekdays), whilst ensuring access to resources including supporting documents and technical information. So, whether you are an operator looking for a one-off water filter purchase for your kitchen, or you are a service engineer looking to stock your van with essential stock for PPM visits, First Choice Group are here to help.
*As tested with E. Coli ATCC (11229). Tested and verified by manufacturer’s laboratory.
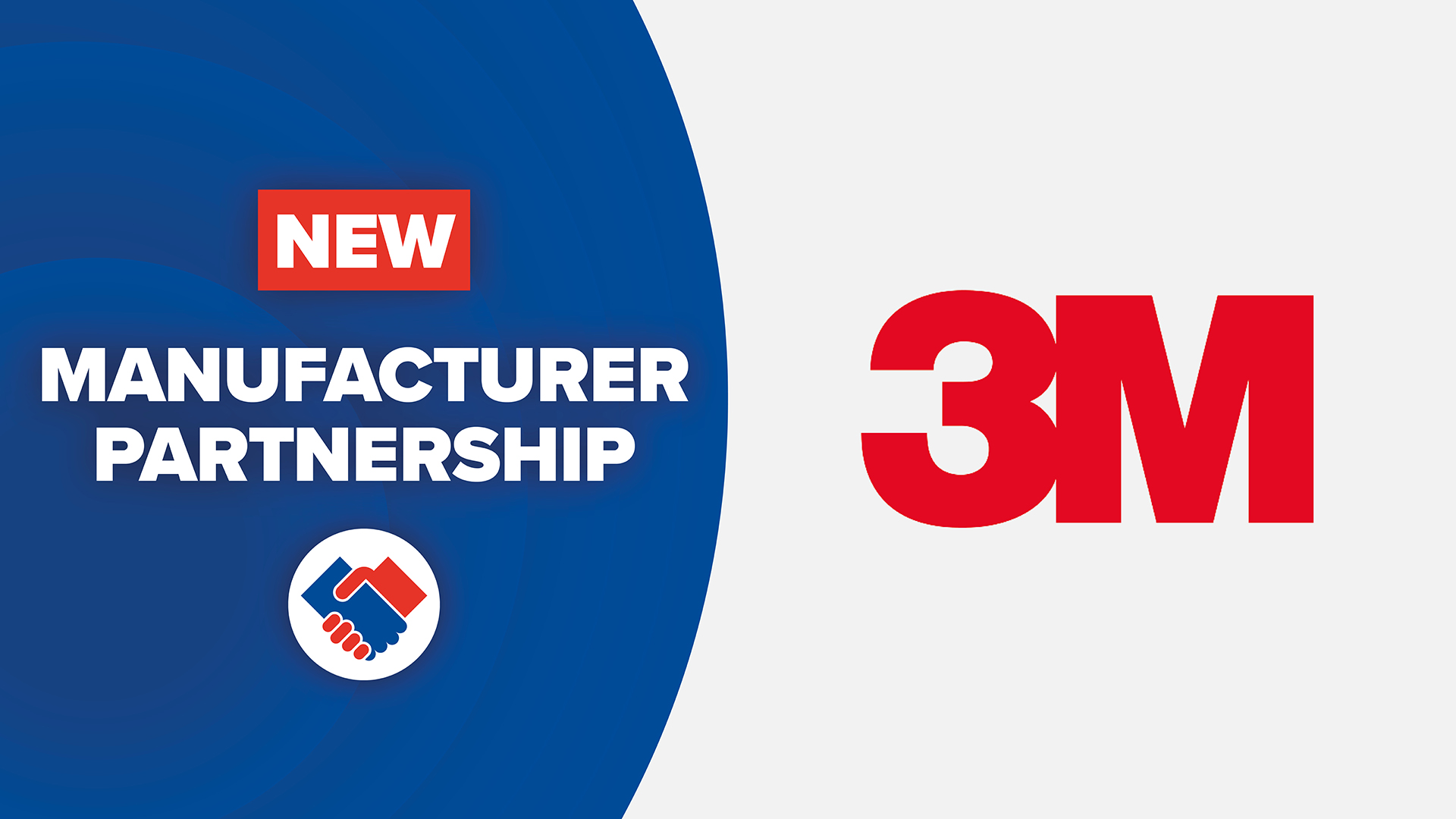
ceda Partners First Choice, Hobart and BRITA Endorse World Quality Day
ceda Partners First Choice, Hobart and BRITA Endorse World Quality Day
Thursday 12th November is the fifth annual World Quality Day and this year, the theme focuses on creating customer value. This is a timely reminder of the importance of truly understanding customers’ needs. At First Choice – working in partnership with BRITA Professional and Hobart Service – we’re committed to working together to meet those needs, not least when it comes to providing good value in the upkeep and maintenance of catering equipment.
Inevitably, 2020 and the COVID-19 pandemic has brought increased stress and challenges to our industry with many more worried than ever about the implications of equipment failure. A recent survey by BRITA Professional of professional kitchen workers found 81% have altered their equipment cleaning and inspection regime post-lockdown. One third are also more cautious about costs due to the pandemic and are looking to maintain and mend equipment where possible,
On World Quality Day, we believe prevention of breakdown has never been more important. This approach will save our customers time, money and ensure operational efficiency as well as having an impact on equipment sustainability.
To celebrate World Quality Day, here are our top three tips on how to maintain the quality of your catering equipment.
1) Always use OEM (Original Equipment Manufacturer) Parts
Catering equipment is the lifeblood of any commercial food service operation, so maximising its uptime is crucial to running a profitable business. As such, it’s essential to look beyond price when caring for your equipment and ensure you put quality first by using genuine parts. The result will be equipment that continues to operate optimally, safeguarding your investment and the people who operate it.
OEM parts also mean you can guarantee high-quality materials and functionality. Such parts keep equipment running exactly as the manufacturer intended, reducing the chances of a failure right in the middle of a busy food service.
2) Preventative Maintenance is Crucial
It’s essential to carry out preventative maintenance such as descaling, deep cleaning and changing water filters on time as this will undoubtedly help improve the performance and lifespan of equipment. The good news is that recent research has found 20% of professional kitchen outlets have recently introduced preventative maintenance, such as a water filter, to prevent limescale build up and damage. It’s essential though that more of us adopt this approach as without it, catering equipment can operate at an ever-decreasing rate of efficiency.
Even with the highest quality equipment it is completely normal for certain parts to degrade with use. Leaving them unchecked could lead to reduced efficiency, higher running costs and, in the worst case, large and costly, avoidable repairs.
As Steve Buckmaster, BRITA Professional Sales Director explains:
“By implementing measures such as preventative maintenance, financial pressures could be eased. For example, on equipment that uses water, one of the most effective ways to prevent premature breakdowns is by using the correct water filter and exchanging it on time. This can help eliminate damage and inefficiency over time caused by the build-up of limescale.”
3) Protect your Warranty
When you buy quality equipment it comes with a manufacturer’s warranty that will help to safeguard you against breakdown but you need to do your part too. First up, ensure that you only use OEM parts as non-OEM parts may invalidate the manufacturer’s warranty meaning the appliance may no longer be covered for future claims. It also means you may not be able to claim back the cost of the part under the warranty as non-OEM parts aren’t covered by the manufacturer.
Preventative maintenance and servicing is also an important piece of the puzzle to ensure you are protecting your warranty and keeping your equipment in the optimum condition possible.
Ultimately Using First Choice Group for your parts and accessories is an extension of the manufacturer’s service and you have access to quality parts from the likes of Hobart and BRITA Professional. This by extension will help to validate claims and reassure you that the supply chain has the manufacturer’s approval.
Customers are at the heart of everything
Embracing quality remains more important than ever as we look to support businesses in light of the pandemic. First Choice, Hobart Service and BRITA Professional all hold the ISO 9001 certification which demonstrates the standards that organisations must have in place within their quality management system.
As an industry we continue to innovate with technology embracing auto replenishment schemes which use APIs so parts can be automatically re-ordered. On World Quality Day 2020 our customers remain at the heart of everything we do as we strive to support you to maintain quality equipment no matter what.
For more information on our OEM spares supply for BRITA Professional and Hobart visit:
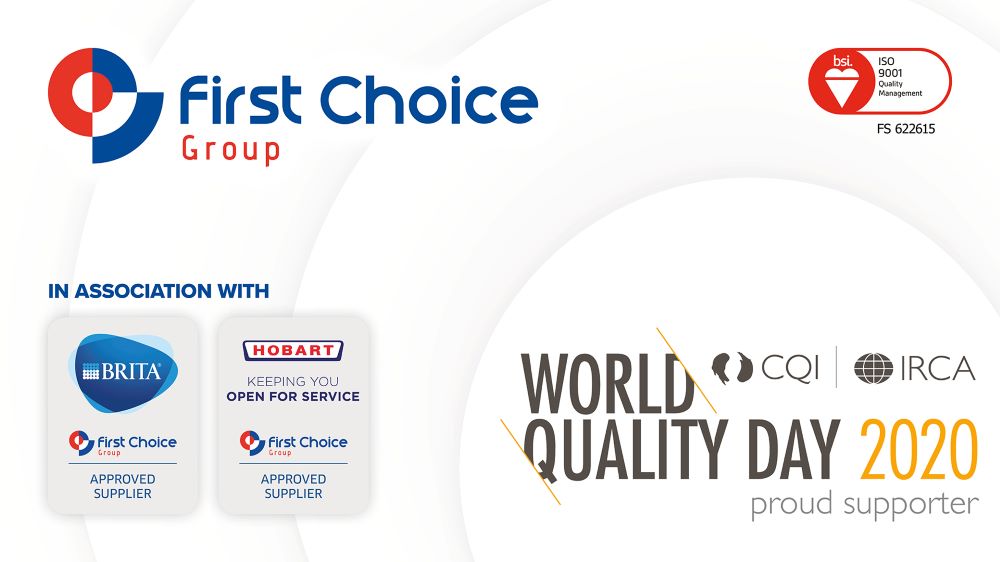
First Choice Group Host CESA & ceda Service Engineer CPD Forum
First Choice Group Host CESA & ceda Service Engineer CPD Forum
First Choice Group are proud to have hosted the first ever Service Engineers CPD, organised by CESA and ceda.
Taking place on Wednesday 9 October, at the First Choice Training centre in Cannock, the event covered a variety of service and maintenance hints and tips, as well as common diagnosis issues and prevalent faults that occur through lack of maintenance.
First Choice Group are recognised for accommodating innovative events at our Cannock base, which acts as an industry hub for catering innovations and updates.
The event was an initiative from the leading trade associations for the foodservice equipment industry. The forum imparted delegates with key information and insight on day-to-day issues through one-to-one knowledge development sessions with manufacturers.
The forum’s content was tailored to Foodservice Equipment Service Managers and Service Engineers with the aim to give engineers an in-depth knowledge and insight to aid them in their daily roles which can be shared with their teams and colleagues.
Our work with these companies allows them to utilise our outstanding conference facilities, providing training and full-day seminars for foodservice professionals to attend and learn more about the industry.
Find out more information about hosting your own event at our purpose-built facilities.
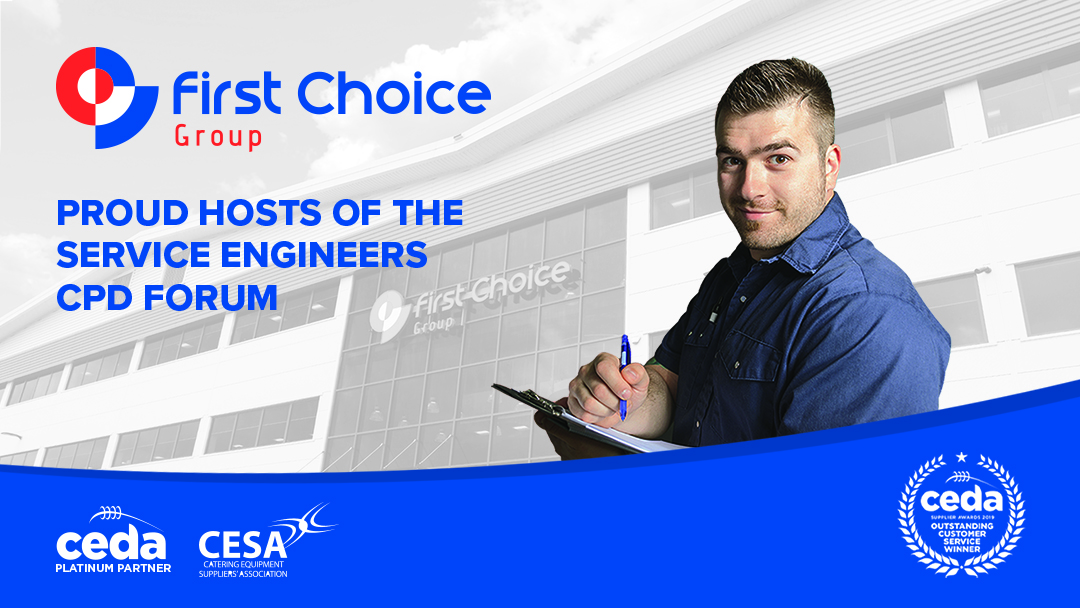
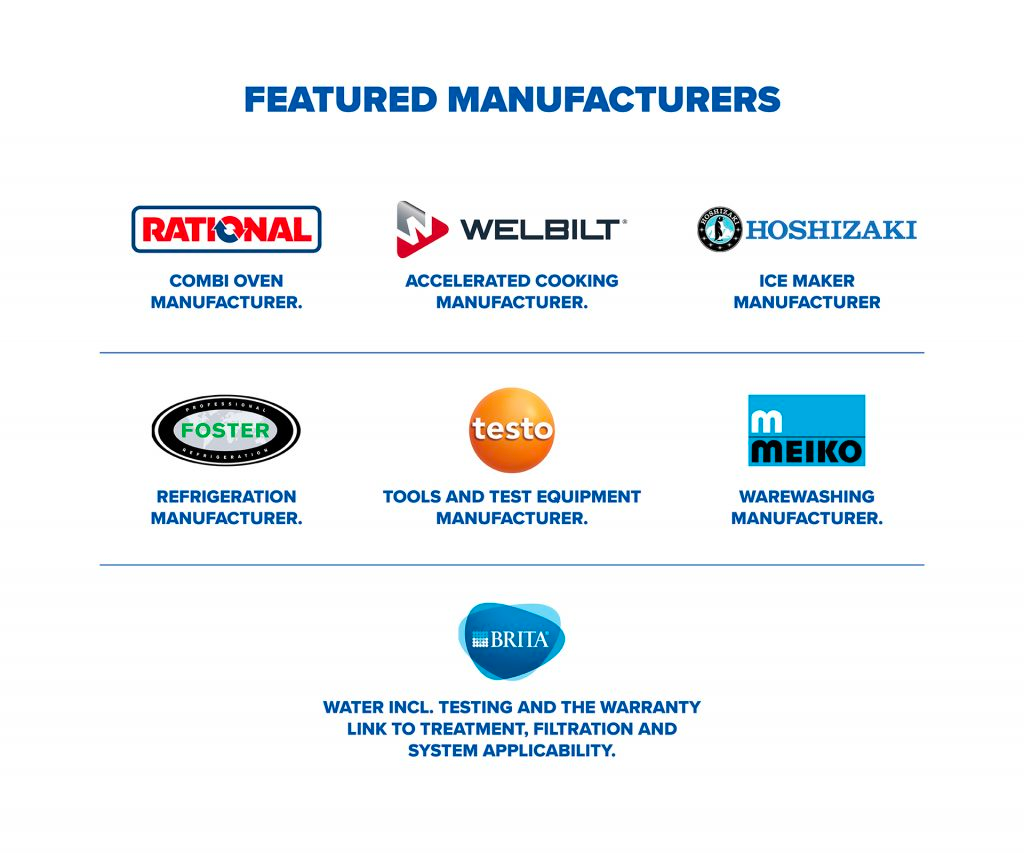