The key ingredients for future proofing your hospitality business by ceda partner Brita
The key ingredients for future proofing your hospitality business by ceda partner Brita
The hospitality industry is finally on the road to recovery following the very challenging times caused by the pandemic. Whilst there is some need to rebuild, many are looking at how they can drive growth and protect their business in the long term.
BRITA Professional recently conducted independent research (1) into the changing perceptions of the industry and where investments need to be made as a result. Here we can share the key results and advice from the research.
[1] 3GEM in collaboration with BRITA Professional (March 2021)
Quality equipment
More than half of those surveyed agreed that investing in quality equipment and maintenance schedules is most important to help future proof their business. This is to ensure that all equipment is reliable and protected against costly breakdowns, so that you can focus on delivering consistently delicious food and drinks with the impeccable service that your customers have come to know and love.
Safety first
As a result of the pandemic, it’s no surprise that an extra focus on hygiene and cleaning is also a priority for almost half of hospitality businesses moving forward. Whilst hygiene has always been at the forefront of the hospitality industry, it’s now front of mind for your customers too.
Customer service is key
With this in mind, customer service is also proving to be a continued priority when it comes to future proofing hospitality businesses, with half (50%) planning to adopt innovative customer service technology and a third investing in ‘Internet of Things’ enabled kitchen equipment.
Embrace technology
Technology is not a new development and certainly not in terms of customer service. However, consumers have come to expect certain conveniences when they shop, travel, and handle their finances — such as mobile access, personalisation, loyalty tracking, and no-touch transactions. More and more, they want their dining experiences to feel the same way (2) and so businesses need to embrace this technology in order to stay ahead or even in line with the curve.
(2) Deloitte: Restaurant of the Future – https://www2.deloitte.com/content/dam/Deloitte/us/Documents/consumer-business/us-consumer-business-restaurant-of-the-future-perspective-final.pdf
Choose the right suppliers who can help your business succeed
Finally, a third of hospitality businesses believe that help from suppliers is essential to achieve greater efficiency across the industry as a whole. Work closely with your suppliers to ensure they understand your needs better and can adapt their services to suit your business. This is becoming increasingly important with the current issues some companies are facing with supply chain and stock availability, which can have a significant impact on your business.
As you can imagine, BRITA Managed Services is passionate about how we, your supplier, can make your life easier. Our tailored packages are offered to relieve some of your pressure and provide services such as ongoing maintenance, advice, monitoring filter usage and carrying out essential filter exchanges in a convenient way that suits you and your business.
For more information about how our bespoke service package can be tailored just for you visit www.brita.co.uk/news-stories/professional/managed-services.
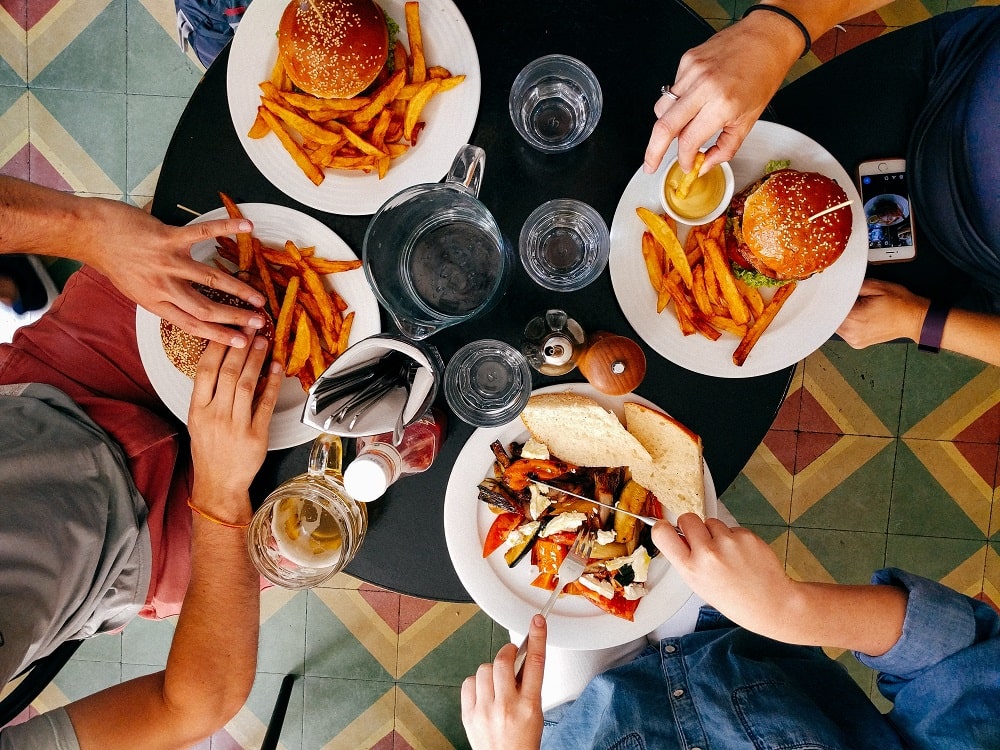
Ceda Partner Brita Professional's New Podcast Series Reveals The Key Ingredients For Business Longevity, From Experts In The Industry
Ceda Partner Brita Professional's New Podcast Series Reveals The Key Ingredients For Business Longevity, From Experts In The Industry
Although the hospitality sector has now reopened, it still faces challenges ahead and operators are looking for support to rebuild their businesses in the long run.
This is evident as new research from BRITA Professional reveals businesses want financial support from the Government (49%), help from suppliers to achieve greater efficiency and cope with rising demand (32%) and support regaining customer confidence (34%).
Looking to the future, hospitality businesses also acknowledge that top quality equipment and customer service will be key to ensuring success:
- 51% say investing in equipment maintenance schedules is most important to help future proof their business.
- Half of business will be adopting innovative customer service technology and almost a third (31%) will invest in Internet of Things enabled kitchen equipment.
- 42% say they will ensure they are able to pivot and respond to change in the future.
- 43% say they will be focusing on hygiene and cleaning.
Alongside this, the key ingredients hospitality businesses believe are needed for future-proofing their business are a loyal customer base (61%), strong teamwork (47%) and the ability to adapt (34%)
These themes and much more are discussed in BRITA Professional’s new podcast series ‘Return, Renew Reinvent’, along with insightful information from industry professionals, sharing how their businesses have responded to the pressures on the hospitality industry to secure ongoing success.
Hear from masters of the industry, including boutique-pub chain YummyPubs, leading training provider HIT Training, coffee roastery Wogan Coffee and catering parts supplier, First Choice on how they have adapted their strategies to invest in their future.
Steve Buckmaster, Director of Sales at BRITA UK said:
“At BRITA we want to support hospitality and catering businesses to invest in their future now the industry has reopened While the pandemic has been an extremely challenging time for the industry, hospitality and catering professionals have demonstrated incredible resilience. Our podcast series brings together voices from across the industry to offer practical advice, first-hand experience and key lessons they have learned while striving to achieve long-term business success.”
Chris Fay C.F.S.P from BRITA Professional explains why preventative maintenance is key to keeping kitchens running smoothly when the industry reopens.
Time-saving SOS: How to achieve optimum kitchen equipment efficiency.
In this article Chris Fay C.F.S.P from ceda Partner BRITA Professional explains why preventative maintenance is key to keeping kitchens running smoothly when the industry reopens.
In 2020 alone, kitchen professionals dealt with 84 days of equipment breakdowns, that’s almost a quarter of the year! As well as having an impact on efficiency and budgets, this is also a huge source of stress. And, at a time when more than eight in ten (81%) professional kitchen workers admit to feeling stressed at work, it has never been more important to take steps to reduce the pressure.
New research from BRITA Professional reveals that almost two-thirds (61%) of kitchen professionals have to manage equipment breakdowns on at least a fortnightly basis. So, it’s not surprising that almost half (47%) believe having more reliable equipment would make their kitchen more efficient when able to reopen. Although unreliable equipment is a longstanding issue, there are some simple steps that staff can take to minimise the risk of disruption to service when the industry reopens:
- Create cleaning schedules: Almost four in ten (39%) hospitality workers would like more robust cleaning schedules to keep the kitchen running more efficiently. Creating a schedule also ensures that the whole team shares the workload – and it feels like less of a chore when everyone is doing their bit.
- Prevent limescale build-up: A high proportion of breakdowns are related to limescale, so preventative maintenance is vital. Limescale build-up not only causes breakdowns, it also means that machinery requires more energy to reach optimum temperatures. Using the correct water filter and changing it regularly will help machines to run more efficiently – and last for longer, as well as eliminating costly repairs.
- Invest in quality equipment: Always choose machinery that meets your maximum needs so that you have the capability to match demand. It may cost more initially, but it’s a worthwhile investment as it will last for longer, saving money over time.
- Outsource maintenance: BRITA Professional’s research found that 35% of kitchen staff say cleaning equipment sends their stress levels soaring. So, it makes sense that a quarter of professionals would like all maintenance to be outsourced to a third party, giving chefs more time to focus on what they love the most: creating incredible food for customers.
- Focus on sustainability: Three-quarters (75%) of hospitality professionals would like to increase sustainability in 2021, with over a third (36%) saying they would like to achieve this by focusing on equipment and energy efficiency. Preventative maintenance can reduce the amount of machinery sent to landfill, so it’s not only an important way to save time and money, but it also helps to protect the environment.
BRITA Managed Services can help to improve kitchen efficiency by supporting operators with a bespoke preventative maintenance package which suits their business needs. By offering advice, monitoring filter usage and carrying out essential filter exchanges, kitchen professionals can rely on their equipment to have a longer life span and deliver a smooth service when they need it most.
The research results are available in a new BRITA Professional toolkit: At Boiling Point: which offers vital tips on how to ‘filter out’ inefficiency and stress, as well as save time, money and the planet in 2021. Take a look at our At Boiling Point Toolkit here: brita.co.uk/boiling-point
0844 742 4940
Twitter: @BRITAPRO
LinkedIn: BRITA Group
#LifeIsBetterFiltered
*All stats in this article relate to research conducted by BRITA PROFESSIONAL and 3GEM among 500 professional kitchen workers (November 2020)
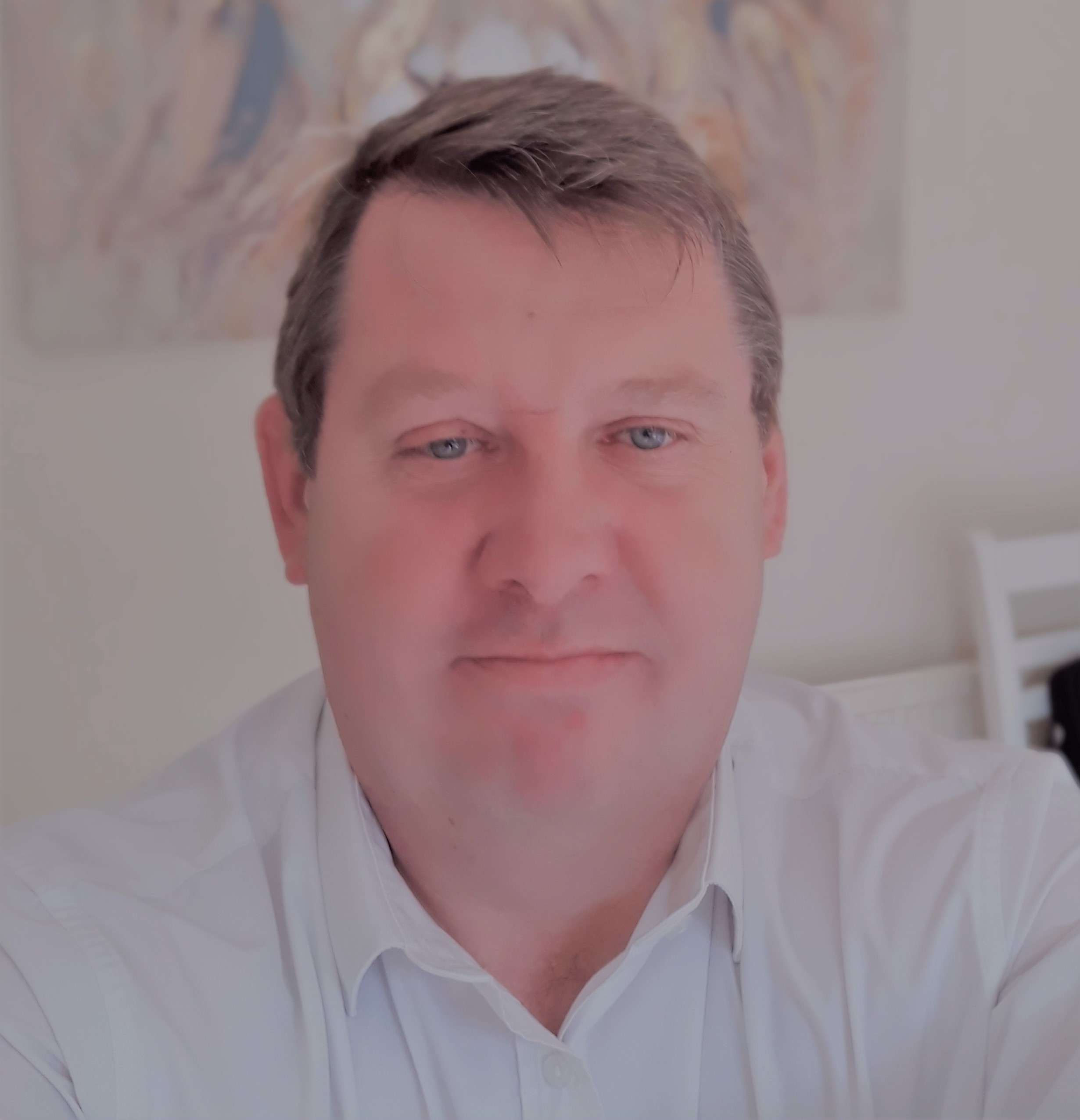
Latest news from ceda Silver Partner Brita Water Filter Systems.
Latest news from ceda Silver Partner Brita Water Filter Systems
ceda members are encouraged to book their place on a virtual Water Training session, run by our Silver Partners BRITA.
Limescale build up leads to equipment breakdown, higher energy costs and also impacts the taste and aroma of food and hot beverages.
Professional kitchens are under more pressure than ever to work efficiently and BRITA’s recent research showed a third of kitchen staff and baristas are being more cautious with equipment to avoid costly breakdowns.
As experts in the field of water filtration and with over 50 years’ experience, BRITA will be offering their guidance and advice in a virtual Water Training session on 10th February 2021 at 10am when you can learn how to effectively protect your equipment while protecting your profitability too.
The virtual Water Training session on 10th February will last approximately one hour and will be hosted by BRITA’s Business Account Executive (Catering) Chris Fay CFSP, who has recently been appointed as a PFS mentor for the FEA. To book your space email professional@brita.co.uk
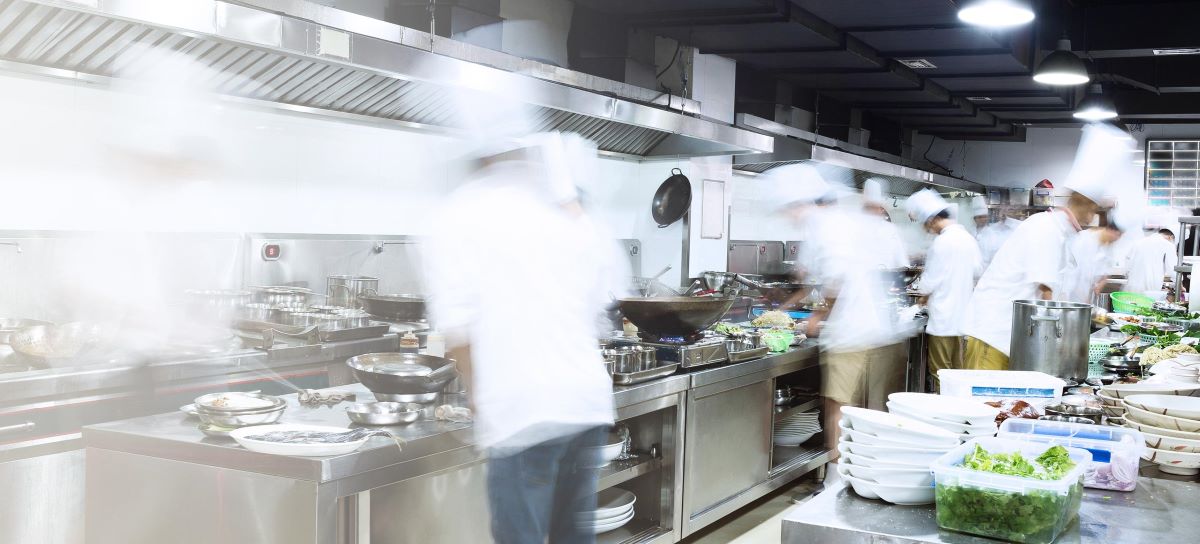
ceda Partners First Choice, Hobart and BRITA Endorse World Quality Day
ceda Partners First Choice, Hobart and BRITA Endorse World Quality Day
Thursday 12th November is the fifth annual World Quality Day and this year, the theme focuses on creating customer value. This is a timely reminder of the importance of truly understanding customers’ needs. At First Choice – working in partnership with BRITA Professional and Hobart Service – we’re committed to working together to meet those needs, not least when it comes to providing good value in the upkeep and maintenance of catering equipment.
Inevitably, 2020 and the COVID-19 pandemic has brought increased stress and challenges to our industry with many more worried than ever about the implications of equipment failure. A recent survey by BRITA Professional of professional kitchen workers found 81% have altered their equipment cleaning and inspection regime post-lockdown. One third are also more cautious about costs due to the pandemic and are looking to maintain and mend equipment where possible,
On World Quality Day, we believe prevention of breakdown has never been more important. This approach will save our customers time, money and ensure operational efficiency as well as having an impact on equipment sustainability.
To celebrate World Quality Day, here are our top three tips on how to maintain the quality of your catering equipment.
1) Always use OEM (Original Equipment Manufacturer) Parts
Catering equipment is the lifeblood of any commercial food service operation, so maximising its uptime is crucial to running a profitable business. As such, it’s essential to look beyond price when caring for your equipment and ensure you put quality first by using genuine parts. The result will be equipment that continues to operate optimally, safeguarding your investment and the people who operate it.
OEM parts also mean you can guarantee high-quality materials and functionality. Such parts keep equipment running exactly as the manufacturer intended, reducing the chances of a failure right in the middle of a busy food service.
2) Preventative Maintenance is Crucial
It’s essential to carry out preventative maintenance such as descaling, deep cleaning and changing water filters on time as this will undoubtedly help improve the performance and lifespan of equipment. The good news is that recent research has found 20% of professional kitchen outlets have recently introduced preventative maintenance, such as a water filter, to prevent limescale build up and damage. It’s essential though that more of us adopt this approach as without it, catering equipment can operate at an ever-decreasing rate of efficiency.
Even with the highest quality equipment it is completely normal for certain parts to degrade with use. Leaving them unchecked could lead to reduced efficiency, higher running costs and, in the worst case, large and costly, avoidable repairs.
As Steve Buckmaster, BRITA Professional Sales Director explains:
“By implementing measures such as preventative maintenance, financial pressures could be eased. For example, on equipment that uses water, one of the most effective ways to prevent premature breakdowns is by using the correct water filter and exchanging it on time. This can help eliminate damage and inefficiency over time caused by the build-up of limescale.”
3) Protect your Warranty
When you buy quality equipment it comes with a manufacturer’s warranty that will help to safeguard you against breakdown but you need to do your part too. First up, ensure that you only use OEM parts as non-OEM parts may invalidate the manufacturer’s warranty meaning the appliance may no longer be covered for future claims. It also means you may not be able to claim back the cost of the part under the warranty as non-OEM parts aren’t covered by the manufacturer.
Preventative maintenance and servicing is also an important piece of the puzzle to ensure you are protecting your warranty and keeping your equipment in the optimum condition possible.
Ultimately Using First Choice Group for your parts and accessories is an extension of the manufacturer’s service and you have access to quality parts from the likes of Hobart and BRITA Professional. This by extension will help to validate claims and reassure you that the supply chain has the manufacturer’s approval.
Customers are at the heart of everything
Embracing quality remains more important than ever as we look to support businesses in light of the pandemic. First Choice, Hobart Service and BRITA Professional all hold the ISO 9001 certification which demonstrates the standards that organisations must have in place within their quality management system.
As an industry we continue to innovate with technology embracing auto replenishment schemes which use APIs so parts can be automatically re-ordered. On World Quality Day 2020 our customers remain at the heart of everything we do as we strive to support you to maintain quality equipment no matter what.
For more information on our OEM spares supply for BRITA Professional and Hobart visit:
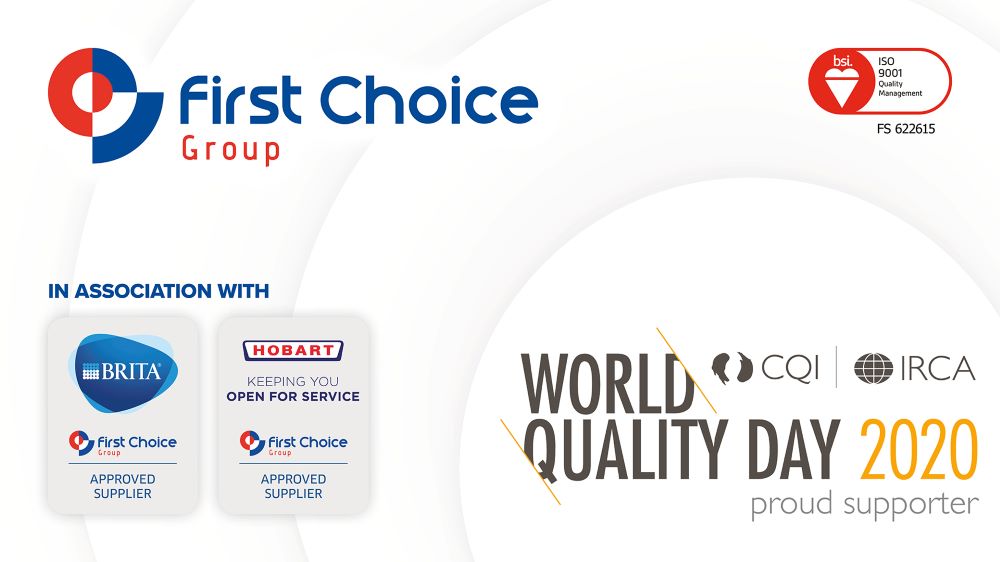